Iron Casting
Release time:
2024-04-08
Source:
Common Application of Fused Ceramic Sand
Fused ceramic sand is mostly used for coated sand, molding and core making, and is suitable for sand mold manufacturers. The common casting processes are: alkali phenolic resin sand, furan resin sand, Pep-set resin sand, shell molding casting process, and being used as raw material for coated sand manufacturers.
What Kind of Factory Will Use Fused Ceramic Sand?
The castings, produced by manufacturers using fused ceramic sand, are usually steel castings, alloy steel parts, or iron castings with high surface quality and precision requirements, which generally have high overall added value. The representative products are automobile and ship parts, such as engine cylinder block and cylinder head, precision valves, mining machinery, etc.
The Requirements of Valve Body- as A Quite Important Part
As an important part of controlling the flow direction of liquid in mechanical equipment, valve body plays an irreplaceable role in modern mechanical equipment.
With the continuous development of modern equipment, the structure and material of valve body are also developing, especially in high-precision equipment with high control requirements. The valve body size positioning on this high-precision equipment is becoming more and more strict, and the internal structure is becoming more and more complex. The traditional coated sand with silica sand as the original sand has gradually been unable to meet the requirements of customers.
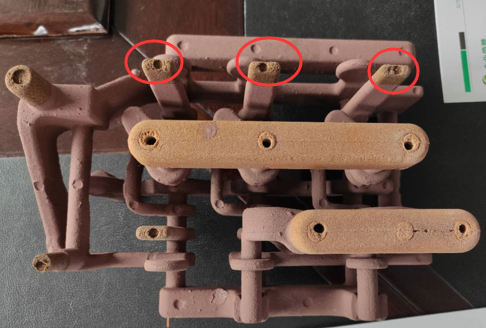
As shown in the figure, the three positions shown in the red circle in the figure are positioning points, and the size error is required not to exceed 2mm. Before using silica sand coated sand for core shooting, the mud core often tilted due to insufficient strength, resulting in casting scrapping due to positioning deviation. Although the strength increases and the positioning deviation meets the requirements after increasing the amount of resin, the casting porosity increases significantly due to the increase of gas evolution, and the scrap rate is still high.
While after the clay core changed into fused resin-coated ceramic sand, the strength of the sand mold was increased by about 30% with the premise that the resin addition remained unchanged, so that the size accuracy of the casting was guaranteed, and the scrap rate of the casting was controlled below one thousandth.
High Demand Valve Body Needs Fused Ceramic Sand
To sum up, on the ductile iron valve body, especially the valve body with complex structure and strict size requirements, fused resin-coated ceramic sand is used to replace coated silicon sand to solve the problems of size positioning and gas evolution at the same time, which greatly reduces the scrap rate of castings, reduces the comprehensive cost of the factory, and improves the market competitiveness of the factory at the same time.
Previous page
Next page
Recent Post
Popular Tags